Case: Albert Knoblinger GmbH & Co. KG The easy and quick way to the required weld seam with the SpeedPulse-XT.
Simple operating concept and excellent welding properties stand out at Knoblinger.
Albert Knoblinger GmbH & Co: KG, based in Ried in the Innviertel region of Upper Austria, has been established in bulk materials plant engineering for decades. The range of services offered by the owner-managed family-owned company with about 80 employees extends from consulting, planning, and design to production and assembly, right through to servicing of the systems. The product portfolio includes plant components for sawmills and chipboard manufacturers as well as scraper and screw conveyors and turnkey wood pelleting plants with an hourly capacity of up to 40 tons. Welding is a core process in the company. More than 20 welding machines are used in its production. Welding units from three popular manufacturers were tested by the company’s own welders in the course of a new investment. The highest priority for selection was that the welders were to be able to achieve the required welding results without much effort and, above all, quickly from the first workpiece. Lorch’s S-series SpeedPulse XT has won out: The extremely simple operating concept of the SpeedPulse-XT was particularly convincing in combination with best welding properties.
Overview of Albert Knoblinger GmbH & Co. KG.
Low-spatter weld seams thanks to dynamic control.
Powermaster torch with ergonomic shape and low weight.
The compact power sources of the S5 SpeedPulse XT series with 400 A that are used at Knoblinger stand out with more than just their excellent operating concept. They also offer impressive welding properties and greatest flexibility. They use patented control technology, a variable arc-length control, and dynamic settings that allow a very individual and absolutely low-spatter welding. The devices are equipped with the water-cooled Lorch welding torch Powermaster MW5900 that is pleasant to handle due to its ergonomic shape and low weight, ensuring fatigue-free welding. The replaceable nozzle holder and the plug-in gas nozzle with gas nozzle seat also allow quick and easy replacement of wear parts.
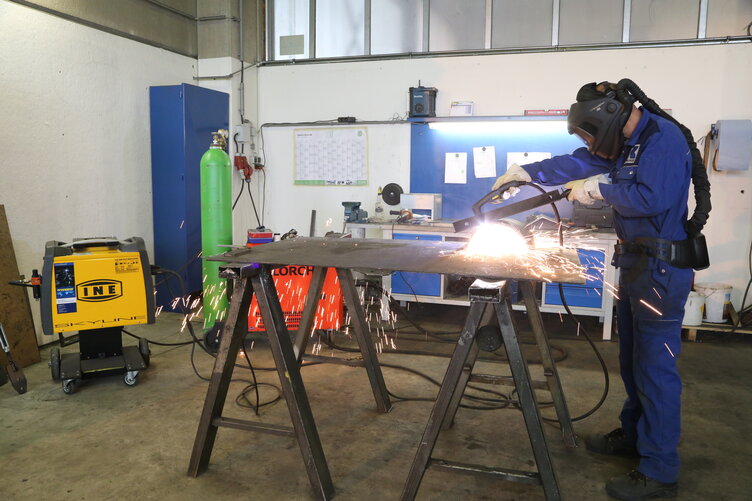
Equipped with all speed processes, the Lorch S-series stands out with best welding properties and greatest flexibility.
The Lorch welding torch Powermaster MW5900 ensures fatigue-free welding with its ergonomic shape and light weight.
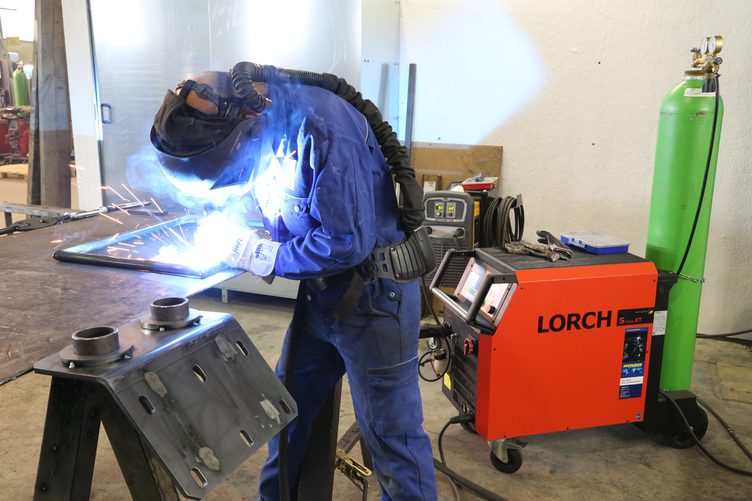
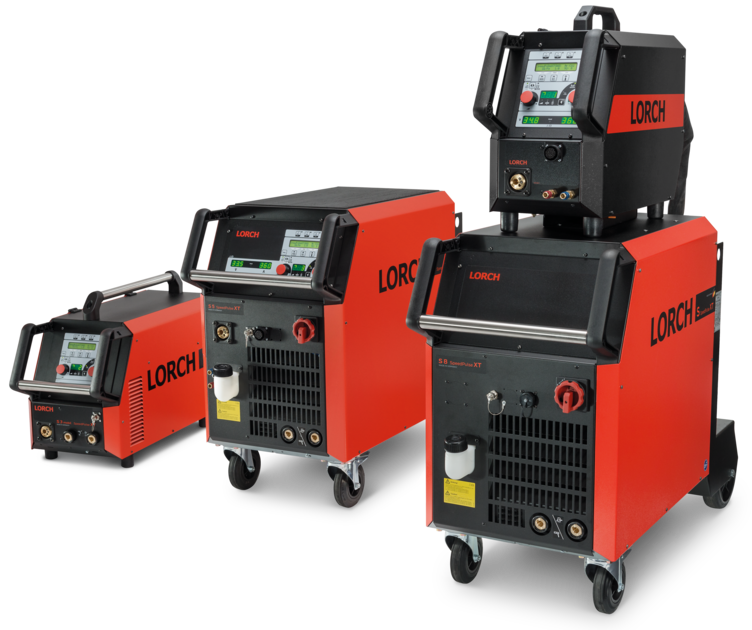
The S-series: Premium MIG-MAG welding units made to measure.
S-series welding units adapt perfectly to your needs, while MIG-MAG Speed processes combine greatest efficiency and quality. Configure the S series precisely to your needs to ensure that your system fits perfectly into the production environment and welding task. On top of this, all S-series welding units are complemented by their intuitive operating concept that provides easy access to all setting options. Learn more now or find a competent Lorch partner near you for personal advice!
Downloads
Do you want to learn more about the Lorch S-series? Technical data as well as further details on application and equipment can be found in the data sheet, and additional information is provided in the brochures: