Case: Messer Industriemontagen & Apparatebau GmbH Efficient welding of oversized parts with the Lorch S-series
Weld seams in constrained positions, such as vertical and transverse welds, are easily controlled as well.
Messer Group from Eastern Hesse has been established in industrial assembly and apparatus engineering for seven decades. Messer’s know-how comes in for the production of huge parts such as evaporators for desalination plants and highest-quality weld seams. The large parts require welding of two thirds of all weld seams as vertical or transverse weld (PF/PC) in constrained position.
Overview of Messer Industriemontagen & Apparatebau GmbH
The S-series stands out with extreme reliability and best weld performance.
Extreme reliability and best weld performance are prerequisites when using the welding units. The company was looking at a wide range of solutions and subjecting all systems to practical tests for four weeks when looking to replace its welding technology. The decision was clearly in Lorch’s favour: The S-SpeedPulse XT stood out with high reliability, a stable arc, and first and foremost its high deposition rate both in the test run and in daily use later.

Extreme demands on weld seam and welding equipment.
Far more than 1000 hours are required for welding an evaporator for the desalination plant. Weld seams must live up to the highest demands, and every single T-joint will be x-rayed individually.
Multi-layer seams are no problem at all.
Precise and clean welding with the S-SpeedPulse XT.

High stability and weld performance thanks to SpeedPulse XT process.
Flexible reaction to general conditions and gap sizes.
The SpeedPulse XT process leads to high stability and weld performance. The variable arc length control gives the welder better control of the pulsed arc, permitting much easier reaction to the present boundary conditions such as different gap sizes by adjusting the torch distance from the workpiece. Difficult welding situations, e.g. in corners, are also easier to handle.
Low-spatter and uncomplicated welding.
Arc length control and dynamic arc control simplify welding immensely.
Additionally, it is possible to set the arc length separately for the start, welding, and end phases at identical current and wire feed. This not only improves weld performance, but also makes the welding process much easier while reducing spatter. “Dynamic control” also allows flexible arc adjustment to the different work tasks and welding positions as well as to the individual welder preferences. This is a great advantage in particular when the parts cannot be moved or rotated due to weight and component size. The dynamic control allows the welders to change the arc characteristics quickly and easily from hard to soft in direct access, adapting them to their individual welding habits.
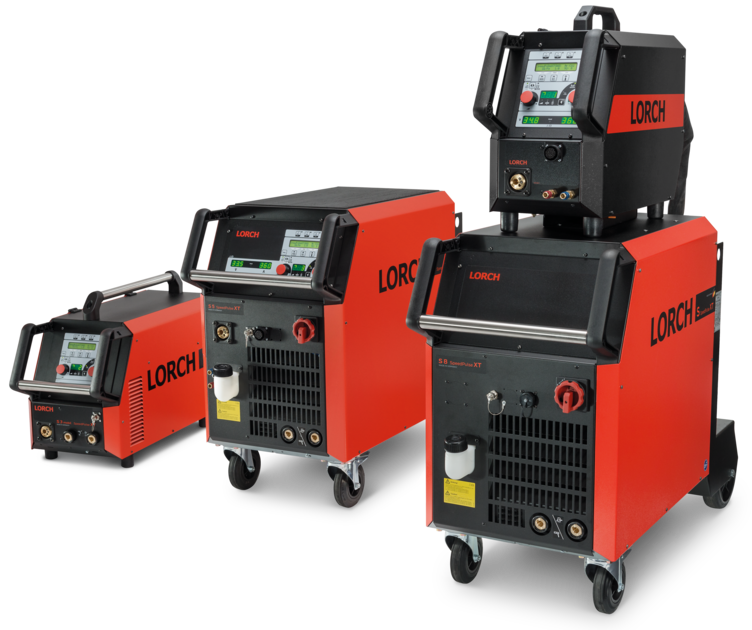
The S-series: Premium MIG-MAG welding units made to measure.
S-series welding units adapt perfectly to your needs, while MIG-MAG Speed processes combine greatest efficiency and quality. Configure the S series precisely to your needs to ensure that your system fits perfectly into the production environment and welding task. On top of this, all S-series welding units are complemented by their intuitive operating concept that provides easy access to all setting options. Learn more now or find a competent Lorch partner near you for personal advice!
Downloads
Do you want to learn more about the Lorch S-series? Technical data as well as further details on application and equipment can be found in the data sheet, and additional information is provided in the brochures: