Case: Stivent Industrie The S-RoboMIG and the SpeedCold welding process combine into an efficient duo.
Special systems for transporting glass or rock wool.
Stivent Industrie near the French city of Poitiers has made a name for itself across Europe with special filter and extraction technology devices. The medium-sized company’s products include a special system that can efficiently transport large quantities of glass or rock wool to all levels of a building via a hose and blower.
Overview of Stivent Industrie.
Welding millimetre-fine steel fast & without distortion.
The apparatus chassis is made up of very thin galvanised steel plates no more than 1.0 to 1.6 millimetres thick, depending on the model. The construction is made up of stainless steel tubes with significantly larger wall thicknesses for reinforcement. These keep the entire device sufficiently stable. Stivent decided to use a combination of the high-performance S-RoboMIG welding system and the SpeedCold welding process from Lorch in order to permit the most efficient chassis production.
As a result, the new robot solution sped up welding by up to 40 percent. Additionally, significant savings in the welding cycle and power consumption were made possible. SpeedCold also extremely reduced the amount of rework required.
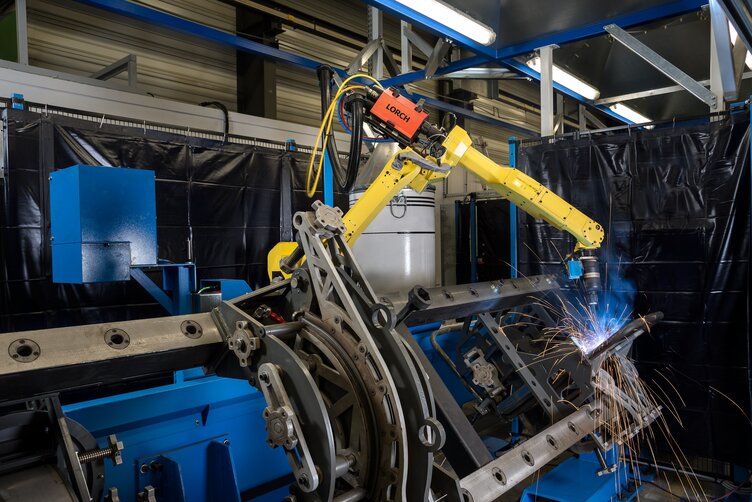
The Lorch robot solution offers high flexibility and an easy start into welding automation.
Stable welding at low heat application thanks to Speed Cold technology.
S-RoboMIG ensures maximum flexibility and first-class, reproducible weld seams.
The SpeedCold procedure, as a special thin-sheet process, controls the process sequence so precisely that it reacts to changes in the arc in milliseconds and ensures excellent weld pool control at all times, even at low energy input. SpeedCold contributes energy precisely matching the requirements in the respective process section, i.e. up to 25 percent less than with conventional MIG-MAG-welding. As a result, SpeedCold has outstanding properties for weld seam modelling and gap bridging. Barely any spatter or material distortion require less rework, thereby adding further advantages. The small amount of spatter remains cold and will not adhere to the chassis, allowing its easy removal with a glove.
The S-RoboMIG robot solution offers the advantage of allowing flexible combination with any robot system from well-known manufacturers. The integrated solution of welding source and robot ensures fast, weld seams of outstanding quality every single time.
Energy efficient welding of thin steel plates.
Thin steel plates with thicknesses between 1.0 and 1.6 millimetres are welded to the base frame. The Lorch SpeedCold welding process only applies the energy currently required.
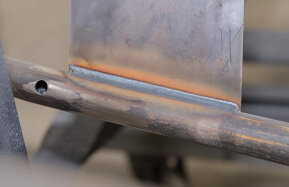

The S-RoboMIG series: Premium MIG-MAG welding units made to measure.
Flexible robot solutions open up new perspectives for industry and medium-sized enterprises. The S-RoboMIG works precisely and is extremely versatile at proper integration, in particular in changing production conditions. The pre-configured, ready-to-weld S-RoboMIG packages for Yaskawa, ABB, Fanuc, Kawasaki, Kuka with torch and interface simplify integration into any production without any coordination great effort with the manufacturers.
Downloads
Do you want to learn more about the S-RoboMIG XT series by Lorch? Technical data as well as further details on application and equipment can be found in the data sheet, and additional information is provided in the brochures: